Lateral thinking
There are many factors explaining why load stability, particularly in the context of road transportation, is more of a focus for testing and research than it used to be even just a few years ago.
Kyle Dunno of the Rochester Institute of Technology (RIT) Department of Packaging Science outlines some of the thinking behind this. “It’s become clear there’s a potentially huge challenge when companies start reducing secondary and tertiary – as well as primary – packaging, and we’ve begun to see different kinds of effect on the stability of loads,” he states. “As more loads are starting to fail, we’re having to ask how we can test for that.”
At the International Safe Transit Association (ISTA), VP technical Eric Hiser says: “The need for a focus on load stability is a natural evolution of the striving towards a truly optimized package. There are always going to be new weak links that you create.”
But he adds that packaging light-weighting is not the sole reason why so much attention is being lavished on load stability. “In Europe, especially, there’s a very heavy focus on human safety, too,” he says, pointing out that this is the case especially in the context of soft-sided vehicles.
If the motivation to understand load stability is strong, it is less clear how it needs to be investigated and tested for. Hiser talks about “wrestling” with the topic, and having done so “for a while now”. “There hasn’t been a consensus with industry on how to approach it,” he says.
To some extent, as with other types of test, questions revolve around the end-point: is the objective to create a tool for root cause analysis or for prediction? Is the aim to optimize the packaging system or to optimize safety?
But in this particular area, the questions are also about what exactly you are analyzing. “There are short impacts, such as running into a dock or forklift handling, but there are also longer-duration events, such as braking and negotiating a roundabout,” Hiser points out. In many of these scenarios, there are multiple dynamics in play. “So we’ve been asking what really causes the problem. Is it one or two events, or is it a longer-duration pattern? Is it a sprint or is it a marathon?”
At IAPRI’s University of Twente Symposium last June, Dunno presented a paper on load stability, and more specifically the characterization of horizontal acceleration events affecting goods in transit. This work is continuing, with sensors being attached to vehicles to capture both the frequency of significant events and the field data signatures which result.
“In fact, although we talk about ‘acceleration’, it’s typically the deceleration that we’re trying to replicate and mimic,” he says. In other words, while acceleration is generally gradual, the deceleration events that RIT is logging span the range from ‘normal’, or gradual, to more aggressive braking and, at the top of the scale, emergency stopping.
“We’re trying to get to the stage where the field-collected data will drive what tests are carried out on acceleration sleds,” Dunno explains.
As a part of its research, RIT is also looking at the stabilizing element in any given pallet-load – typically the stretch film. “We’re trying to look at how film is applied to a load and, if we apply film in a certain manner, how that affects the response of the load,” he says. “Not many academic institutions are focused on the role of film application.”
Dunno also contributes to the ISTA Load Stability workgroup, characterizing its investigations into shearing and the responses of individual layers in the load as being “really the opposite of what I’m trying to do with stretch film”.
Fellow IAPRI members Smithers MSE Limited (formerly, Smithers Pira) and Michigan State University (MSU) School of Packaging have worked with ISTA on the project. MSU developed an ‘artifact’ with multiple, mobile layers able to measure the response of each level to specific horizontal impacts, with Smithers running ‘proof of concept’ tests at its Lansing, Michigan, site.
The MSU artifact has since been named the Simulated Unit Load with Integrated Instrumentation (SULII), with SULII 2.0 having been extended to up to six layers – or to the height of a full palletized load.
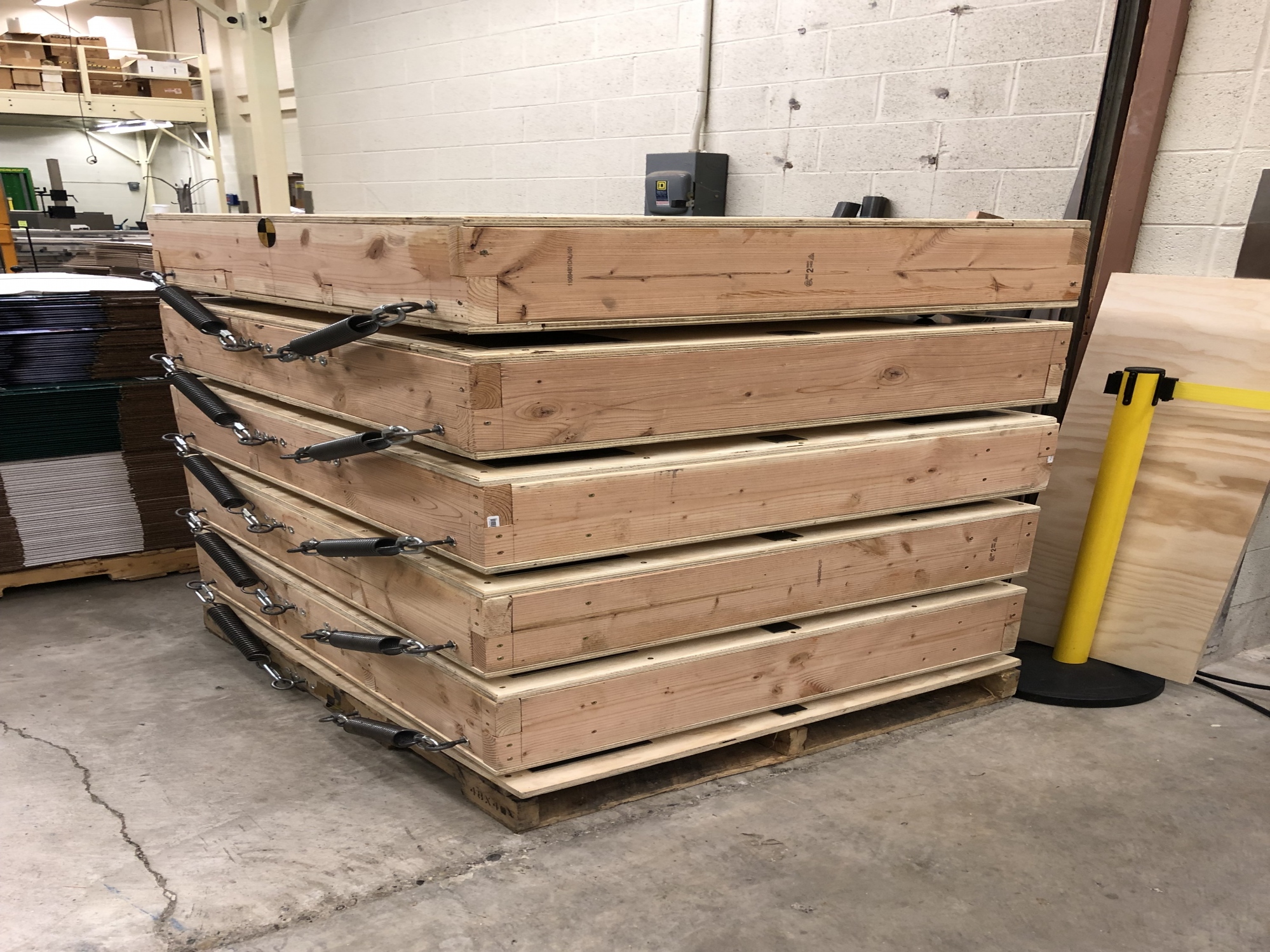
Patrick McDavid at MSU explains: “Our hope is to come up with a way to record unit load stability in the real world, and then recreate those forces in a lab. This grew from a need to utilize a recently-installed incline impact tester at the MSU School of Packaging.” Because of the amount of testing required, MSU developed a system that could be reset and reused, rather than being destroyed with each test.
“Unlike real unitized loads, which shift from the effects of horizontal impacts and long-duration/low-G forces, SULII’s springs and rollers reset each layer after each event, and return to center,” says McDavid. Each layer can also be fitted with accelerometers, allowing pallet-level forces to be compared with top-level forces.
“Current testing was recently performed with SULII 2.0 over a short-duration, controlled-delivery trip, and the data is currently under analysis,” he says. “We are already thinking about improvements to make for SULII 3.0.”
Hiser at ISTA reports: “We ran a small, semi-controlled field study to see whether we can get clean information or whether it’s all going to be ‘noise’.”
As well as raw data from SULII, video material was also obtained from the field trial on board a Green Bay Packaging truck.
Dunno at RIT contrasts the ISTA focus on shock-related, short-duration, high-acceleration events with his own on longer-duration events. “Both are looking at horizontal impacts,” he points out. “Both matter, and both need to be evaluated.”
According to ISTA, discussions around the use of SULII for short-duration impact work have already inspired several other research proposals, including some relating to longer-duration events and prolonged acceleration/deceleration.
Now, ISTA has plans to push the MSU/Smithers investigations out among its wider membership. “We will likely be making a call for members to collect their own field data specific to this topic of load stability,” says Hiser. “And we will be funding a small confirmatory study.”
Part of the role of the ISTA confirmatory study work is to act as a benchmark and point of comparison for other data that may have been collected in this area.
“Our ultimate goal is to bring clarity to this topic and suggest the best tools with which to do this,” he says. “Ultimately, we want to bring forward a method or multiple methods that will help companies reduce product damage and packaging waste throughout the supply chain.
Many in industry and in the research and testing community will be eager to contribute – and to see what tools and methods emerge.